1. CAD: 3D model + 2D
drawings
|
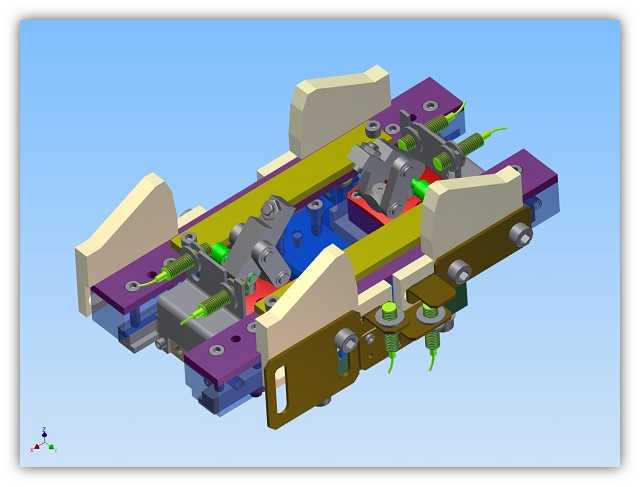 |
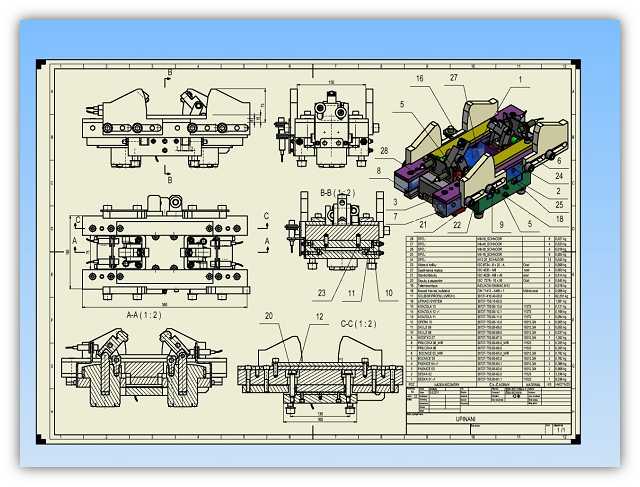 |
2. CAE: simulation of load behavior
|
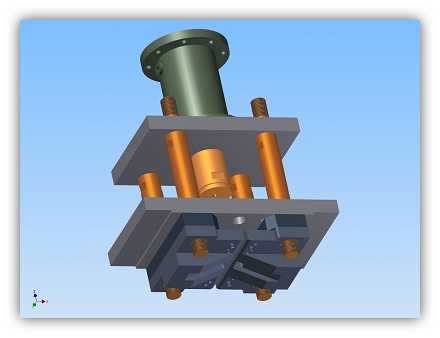 |
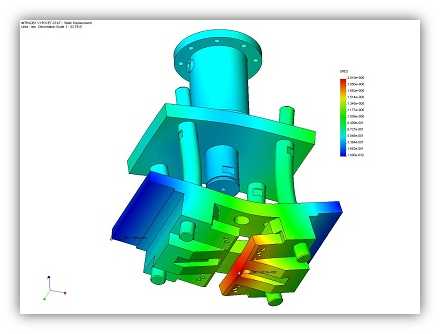 |
3. CAM: we carry out production on modern CNC machine tools
|
C
400 HERMLE
- machinig center for 5-axis machining
- control system Heidenhain TNC 640
- max. rotation speed:18000 ot/min
-
linear shift X/Y/Z 35 m/min
- platen 1070x700 mm
- travel line 850x700x500 mm
- weight load of the table 2000 kg
|
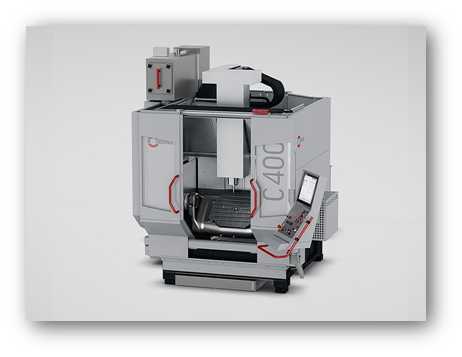 |
DMG
MORI NLX 2500/700
-
turning center for 6-axis machining
- control system CELOS
- tool rotation 10000 ot/min
- workpiece d = 80 mm, l = 200/705 mm
- workpiece weight max. 250 kg
|
|
FANUC Robocut -
C600iA
- electroerosion wire EDM FANUC
- high quality cut surface Ra 0,15
μm
- workpiece weight 1000 kg
- machined size 600x400, Z-axis 310 mm
- max. taper angle 30°/150
mm
- min. programme step 0,0001 mm
- wire diameter 0,1-0,3 mm
|
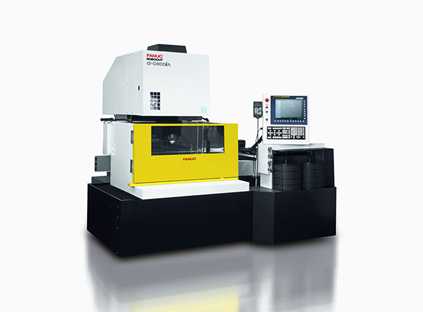 |
Engraving LASER HXP
20E
- marking produced parts 110x110 mm
- rotary axis for marking on cylindrical surface
- LASER power 20 W
- min. line width 0,02 mm
- min. character size 0,2 mm
|
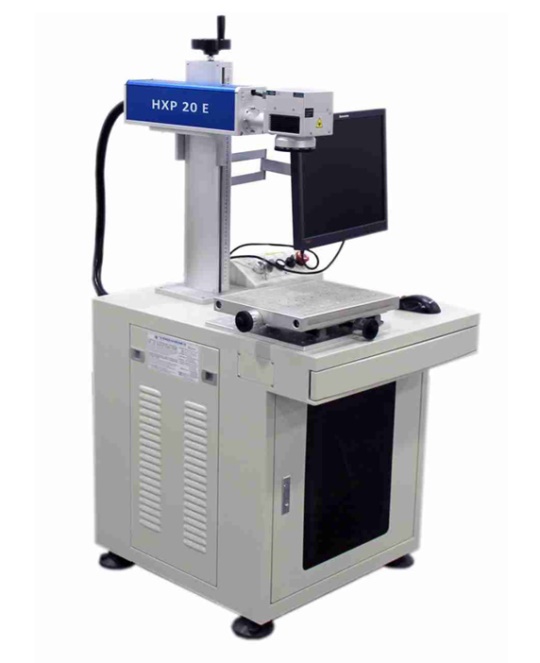 |
4. Heat treatment and coating
|
Vacuum hardening
We use vacuum hardening when hardness and toughness of shear tools are
required.
Vacuum heating is followed by cooling with nitrogen gas, so there are
no dimensional changes and the surface is not scaled.
|
Nitrocarburizing
Nitrocarburizing
is a surface treatment, a thermochemical diffusion process meant to
provide an anti-wear resistance on the surface layer, to improve
fatigue resistance by up to 120 % and to improve corrodion resistance.
It
is carried out at temperatures up to 600 °C, which minimizes
deformations and creates a tough core with a hard case layer up to a
thickness of 50 μm.
|
Blackening and zinc coating
All
steel working parts are surface treated by alkaline blackening - an
oxide layer forms on the surface, combined with oiling creates a proven
surface protection.
Additionally there's an option of galvanizing and blue passivation.
|
Powder coating (komaxit - RAL colour
standard)
External
covers and visible parts are treated by electrostatic application of
powder paint. WHen heated to 180 °C, hardening occurs and a
high-quality surface layer is formed.
|
5. Welded frames manufacturing
|
For
the purpose of manufacturing supporting frames and testing of the
assembled production lines we have 2 big manufacturing halls at our
disposal, including a fully equipped locksmith workshop.
|
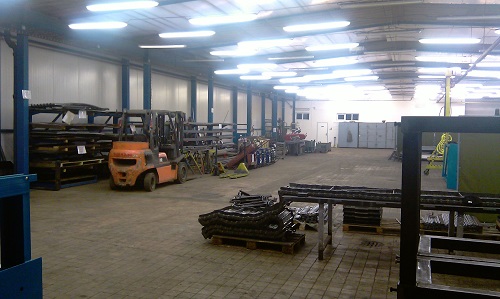 |
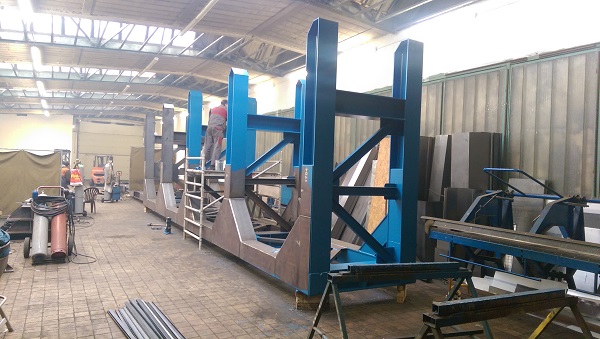 |
6. Completion + assembly
|
Main assembly
of machines and lines up to 10x10 m is carried out in a separate
manufacturing hall.
|
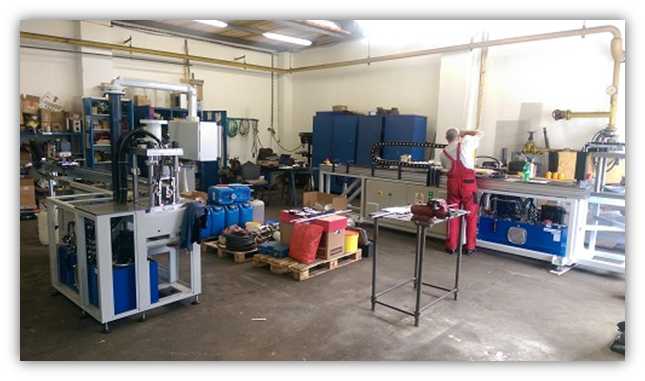 |
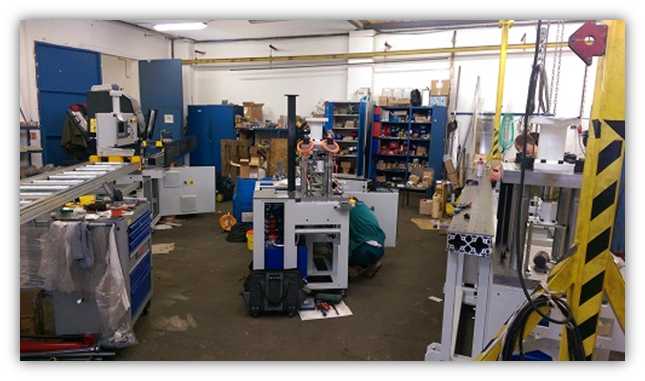 |
7. Despatch
|
Machines and lines are
despatched onto the loading area of trucks in the indoor environment of
the manufacturing hall.
|
|
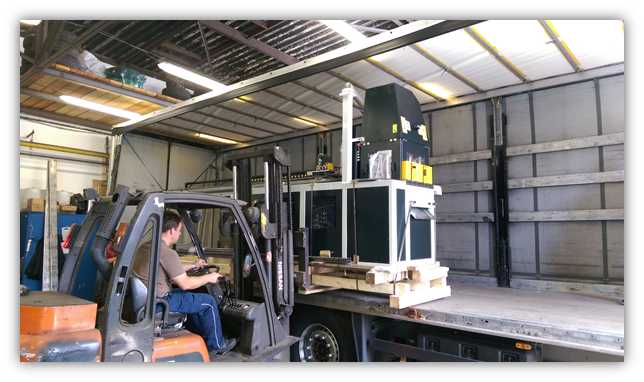 |